Energy Efficiency of a Chiller Plant
Real-world chiller plant efficiency with VSD and Chiller Manager was measured best at 0.84 Kw/ton average. Where the best chiller plant could be targeted at 0.65 Kw/ton average (22.6% better). This point cannot be reached with the use of hardware (Variable Speed Drive with the Chiller Manager or Building Management System). Why? Because the major factors which determine the optimum chiller plant efficiency, were not native part of said hardware. The mention factors are:
o Reducing the hydraulic pipe friction or bottle neck that once, necessity for HVAC commissioning/hand over period
o Use of smart/intelligent software capable of managing the summation power of all plant components (Chilled water pumps, chillers, condenser water pumps and cooling towers) to be as low as possible with actual loads and climates throughout the day, at the same time, the cooling output must be maintained. Almost all VSD installers failed to this point as simple pressure sensor/temperature control will not do the job.
o Use of intelligent thermostat for all AHU. When the “Energy Efficiency system” was running, the feedback from all the air-conditioned sensitive areas must be continuously monitored. Once the tendency the room conditions is out of controlled, the “Energy Efficiency system” must be able to response immediately and correct the problems without human intervention. Such situations could occur at least once every day. This is where the intelligent thermostat can be used to communicate with the chiller plant controller.
Basic concepts
The chiller plant capacity is designed for 100% load at a standard design condition (25C room and 35C ambient).
If a chiller run at 100%, the ancillary equipment run 100%. This condition may give the desired energy efficiency level.
In real world, the ambient temperature changes hourly, also the load. This off-design condition is inevitable. If a chiller run at 60%, the ancillary still run 100% (as no control is provided). At this point, the pumps and fans, wasted 67% energy more than they should be.
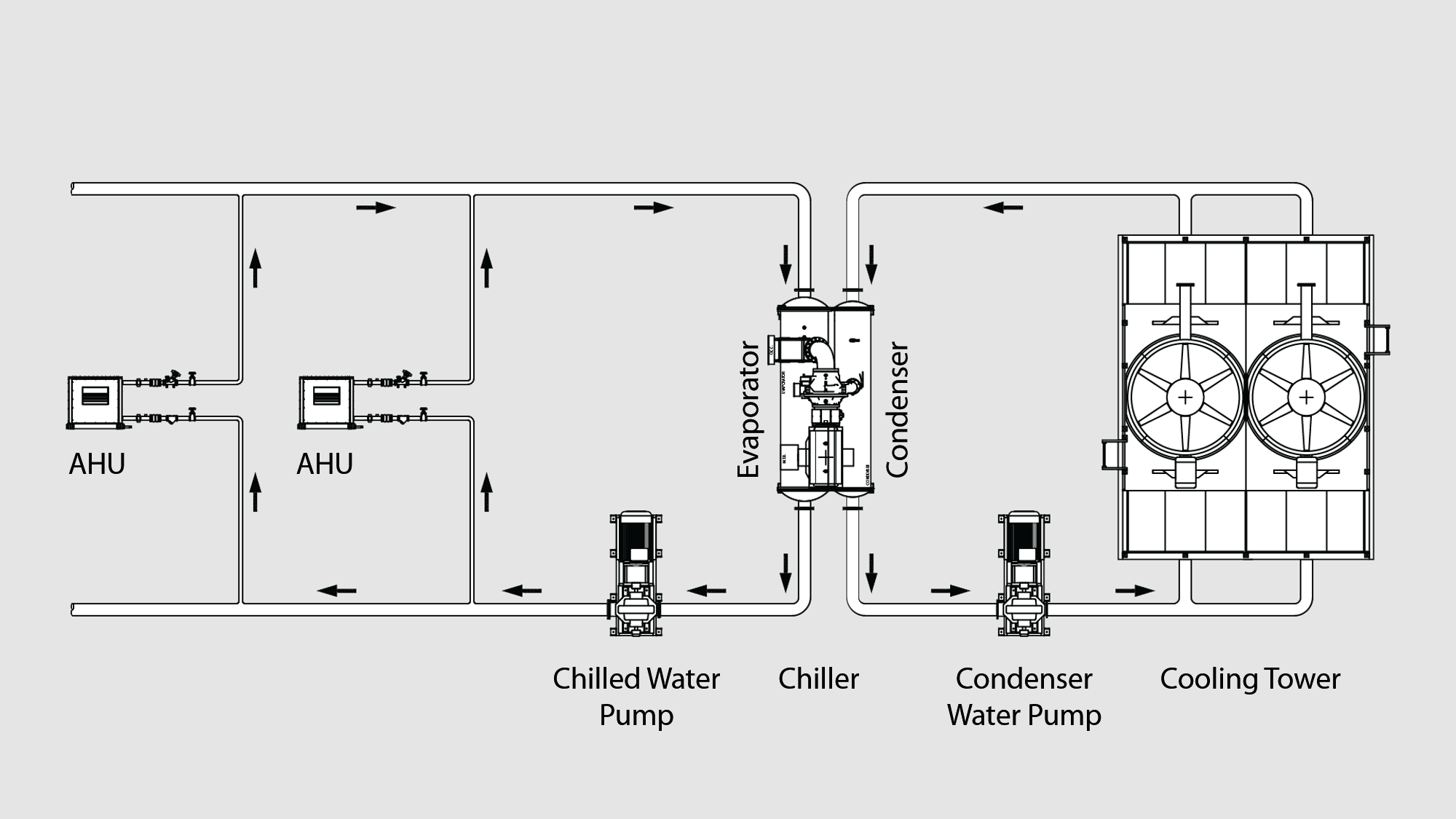
Chiller Plant Piping Diagram
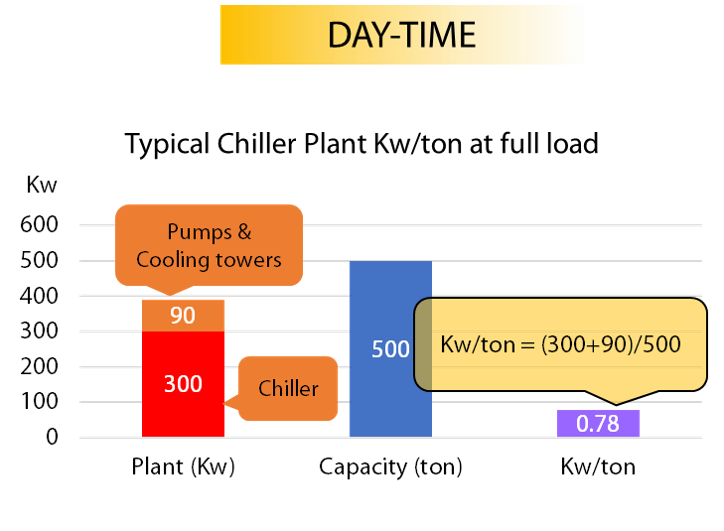
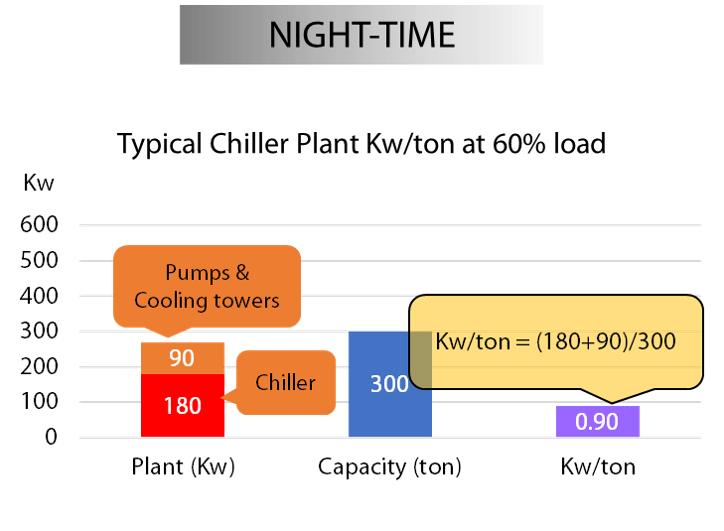
Typical Chiller Plant with VSD and Chiller Manager
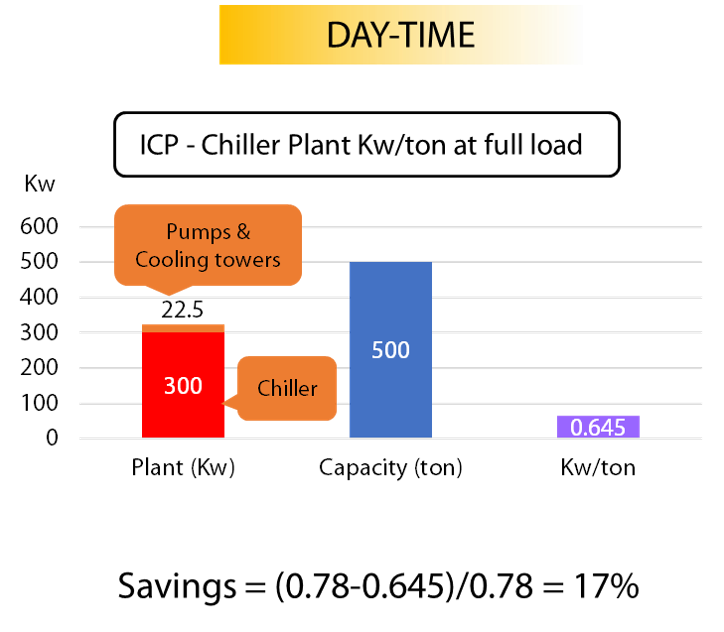
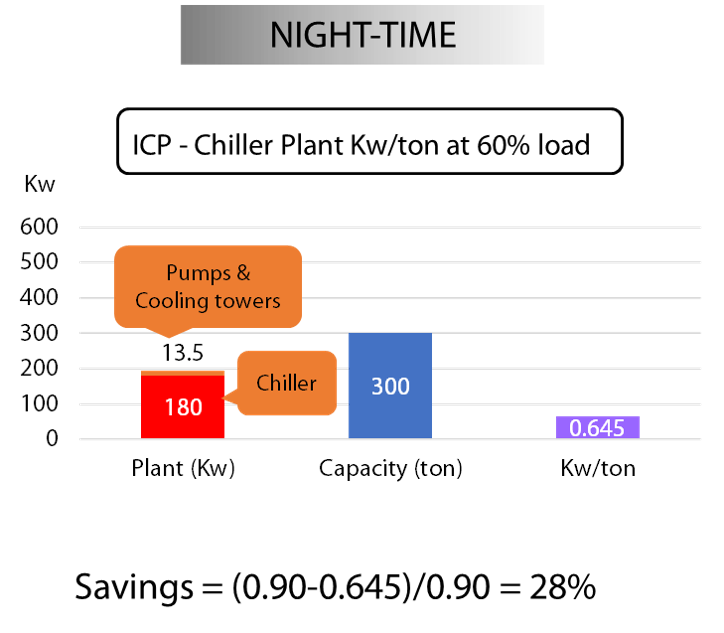
Intelligent Chiller Plant
Intelligent Chiller Plant
A simple speed control might be used to maintain the plant efficiency. However, there usually more than one chiller with many pumps and fans plus spares. During the change over, such simple speed control cannot accommodate this situation, causing the plant shutdown. This is where the Intelligent Chiller Plant come to exist.
Most of the Chiller Plant Manager (CPM) control panel screen is full of information (temperatures, pressures, frequency, power and so on. It may be useful for a facility manager to see if the plant operates as normal or if something went wrong.
The Chiller Manager is also useful as a tool to control plant operating parameters remotely in order to save energy. More or less energy savings depends on individual skills and know-how of the operators. It also requires a person or an energy expert to be there all the times.
The Intelligent Chiller Plant (ICP) screen is in one way, much simpler. It contains only useful information arranged for the user to be much easier to use. Brief of different points of the Basic chiller Plant, CPM and the ICP are as follows:
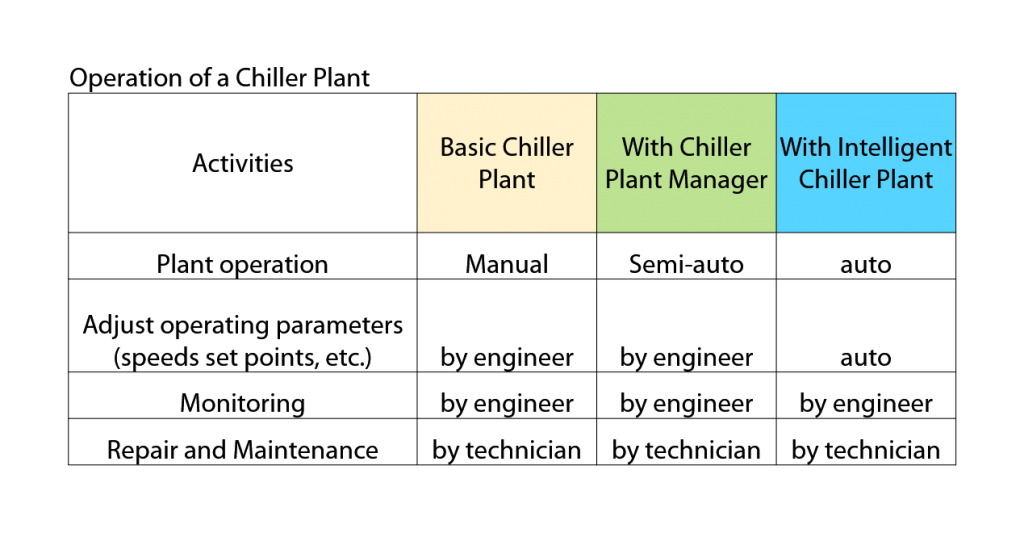
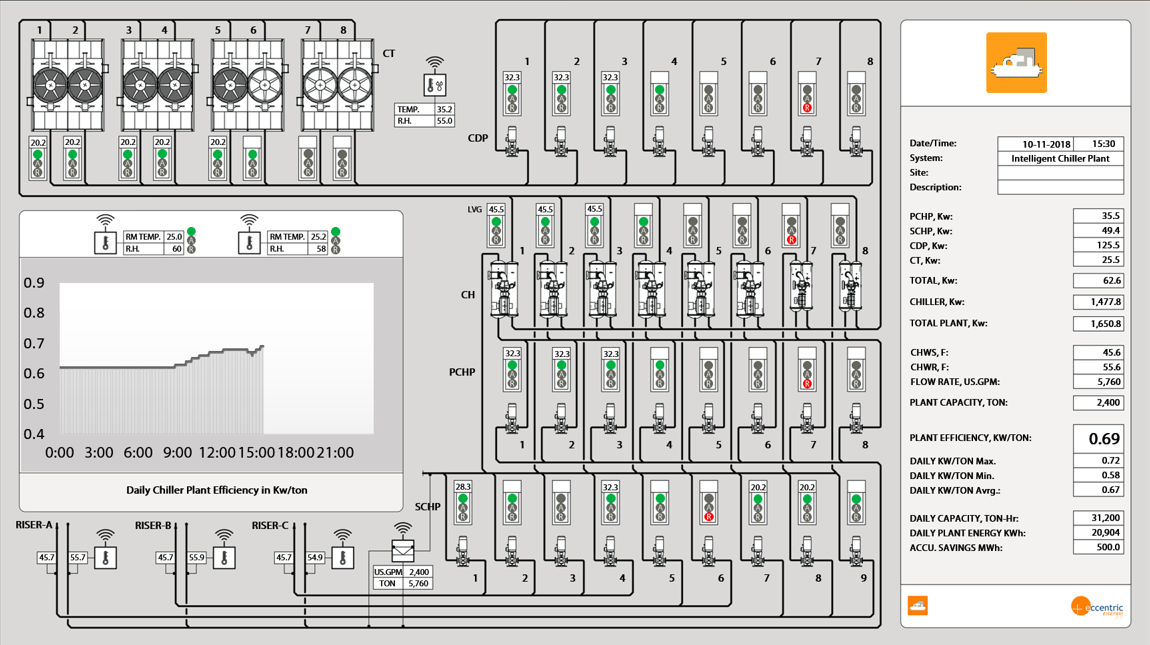
ICP Screen of a large chiller plant
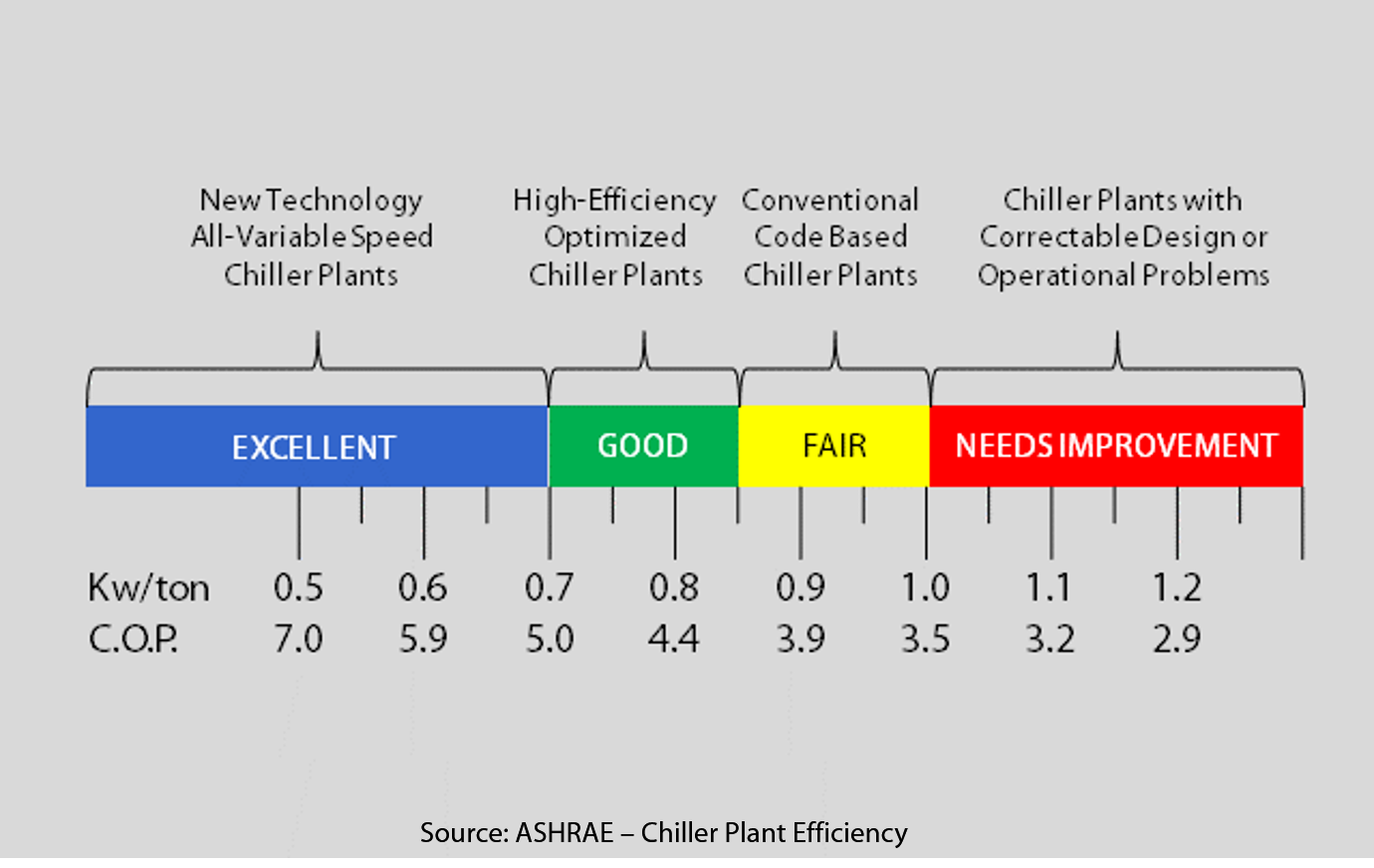
List of energy efficiency improvement areas
The chiller plant energy efficiency improvements can be listed as follows:
CHILLER PLANT
Cooling tower speed control and operation management
Condenser water speed control and operation management Control floating chilled water set point Control chiller operation and management to operate at best efficiency range all the times
Control primary chilled water pump speed
Control secondary chilled water pump speed
Measurement of energy consumption and cooling capacity to determine Kw/ton all the time
Monitor end user’s critical areas and have the chiller plant response in-time
Show warning/alarm if the chiller/cooling tower efficiency dropped and require
cleaning
HYDRAULIC BALANCE
Control differential pressure of chilled water loop
Re-balance the chilled water loop for energy efficiency
DEMAND SIDE
Use thermostat with temperature profile function with centralized control
Use thermostat with real-time efficiency monitoring for each AHU
Control all room humidity at optimum for all seasons
Use carbon dioxide sensors to control fresh air intake
Use occupancy sensor to turn-off fan-coil unit